From 5 to 9 December 2022, the Agricola University of Applied Sciences (THGA), together with car repair shop employees at a Vergölst branch in Bochum, collected data for the first time using a Car Repair 4.0 measuring computer. Read about how exactly the measurements took place on site.
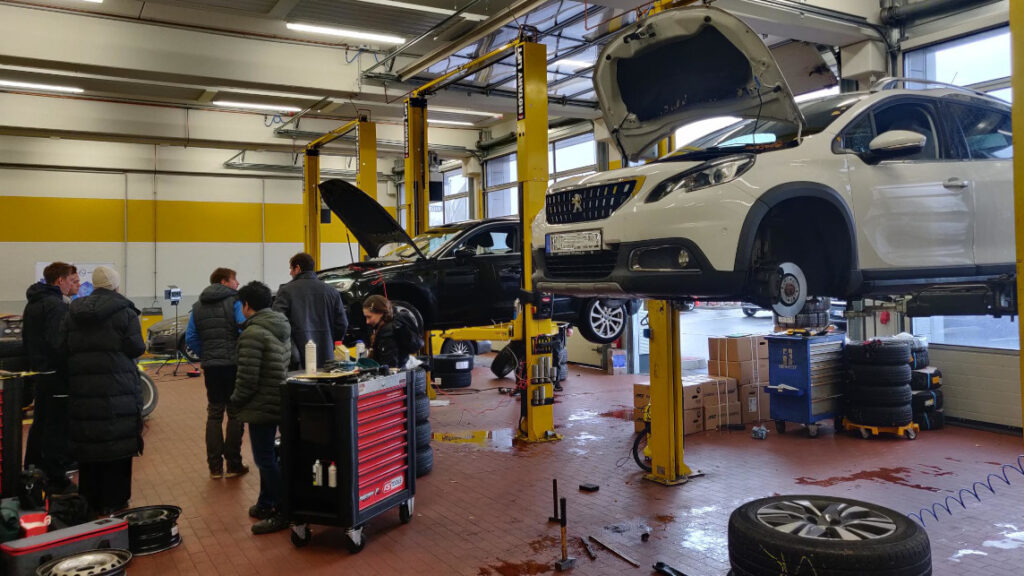
By Ralf Schädel, IT Editor and Project Manager Cloud Services and Gaia-X at eco – Association of the Internet Industry
Trace the data history and check for errors: This was the focus of the measurement week organised by Car Repair 4.0 at the Vergölst car repair shop on Dorstener Straße in Bochum. After the Car Repair 4.0 measurement professionals demonstrated the complete data transfer from the collection on the vehicle to the AI-supported diagnosis for the first time at the milestone meeting last month in Osnabrück, the next step in the project development now followed. By measuring the voltage at the battery, THGA and car repair shop employees jointly collected data and checked or evaluated its path to the cloud.
Battery measurement is just the beginning
The project team chose the battery or voltage measurement method because it is easy to implement and, based on it, data from other measurement recording points can also be tapped in the future. Thus, it is hoped that the data from the start-up process that has now been measured will provide further insights for error diagnosis: “If anomalies are visible in the voltage curve, they may allow conclusions to be drawn about components such as the engine or the alternator,” explains Magnus Komesker, research assistant at the Osnabrück University of Applied Sciences (HSOS).
Measurement template specifies procedure and instruments
Before the measurements could begin in Bochum, the partners from Auto-Intern, DEKRA, DFKI, HSOS, THGA and Vergölst first drew up a measurement specification. In it, they specified that there would be two measurement runs during each starting process with energy consumers such as the auxiliary heating or music system switched on and off. The choice of measuring instruments fell on an Omniscope and a Rasperry Pi as the measuring computer. The German Research Center for Artificial Intelligence (DFKI) also made sure that there was dual labelling: Whether a car was on site because of a defect or a defect only became visible in the measurement.
Create conditions for hardware and the car repair shop
With the measuring computer, the foundation was laid on the hardware side so that all components to be measured, such as the Omniscope and the software, could be integrated and their functionalities taken into account in the measuring setup. The task of the software is to ensure the transfer of data to the server or the cloud. A special challenge: As WiFi was not available everywhere in the repair area. Therefore, the measurement experts also planned an offline operation.
Everyone was satisfied
After careful preparatory work, the measurements finally started: Around ten car repair customers per day jumped at the chance to have the error memory of their vehicle read out free of charge and the result sent to them by email. A service that can normally cost up to EUR 70 at car repair shops. But it was not only the participants who were satisfied. “From the process of the battery measurements carried out to the testing of the measurement system and the feedback from the users; the whole process was coherent,” says Magnus Komesker.
Helpful feedback from users
The mechanics shared with the Car Repair 4.0 team that just three clicks during data acquisition was a negligible additional effort of one minute. With the oscilloscope recording and the subsequent AI-supported diagnosis, the usual measurement method via the OBD interface is usefully supplemented. And on top of that: “The Vergölst employees gave us important information that the handheld device is intuitive to use, but that we should still make small changes to the user interface with regard to the touch buttons,” says Komesker.
Conclusion: The Car Repair 4.0 team has thus demonstrated for the first time that it can collect data from vehicles in operation in a standard car repair shop and record additional data such as mileage. The data acquisition and forwarding, which will later be done to the Gaia-X platform, worked well, and the data being transferred to this data-sovereign space was not lost. The Car Repair 4.0 team is already looking forward to the next step in the project when the data collected will be made available to the DFKI. Then a neural network can be trained, and further test cases for sensors can be recorded.